Aby końcowy produkt miał wysoką jakość oraz charakteryzował się bardzo dużą odpornością na trudne warunki atmosferyczne, oprócz tzw. "bazy" czyli tworzywa sztucznego (PVC), "wypełniacza" będącego mączką drzewną, komponentów "uzupełniających" oraz niezbędnych komponentów wspomagających sam proces produkcyjny, koniecznym jest także aplikacja wysokiej jakości koncentratów barwiących popularnie nazywanych MASTERBATCH.
"Baza" - tworzywo sztuczne (PVC)
Charakteryzuje się dużą odpornością na korozję, chemikalia, oleje i czynniki atmosferyczne. PVC-U posiada dobrą wytrzymałość na rozciąganie (do 50 MPa), zginanie i ściskanie (nawet do 100 MPa). Występuje w dwóch odmianach: czyste, tzw. Pure PVC, nie przetworzony surowiec o wysokich właściwościach fizycznych oraz przetworzone, tzw. Regranulat czyli zmielone odpady produktów wytworzonych uprzednio z czystego PVC, mające pierwotnie inne zastosowanie np. rynny, rury, uchwyty, parapety, okna, drzwi i inne. Jakość tego komponentu mocno wpływa na właściwości fizyczne i odporność gotowego produktu.
"Wypełniacz" - mączka drzewna
Rozróżnia się dwa rodzaje mączki drzewnej, w zależności od gatunku drewna z jakiego jest wykonana. Pozyskiwana jest ona z drzew liściastych i drzew iglastych oraz występuje w kilku frakcjach (grubość ziaren mierzona w mikrometrach). Z powodu dużej kancerogenności drzew liściastych, rzadziej stosowanym wypełniaczem jest mączka pozyskiwana z tego rodzaju drzew. Znacznie częściej stosowaną mączką jest mączka z drzew iglastych.
Frakcja mączki to już indywidualny wybór każdego z producentów oparty o filozofię sprzedaży i postrzegania estetyki wyrobu, ponieważ im większe cząstki drewna, tym bardziej widoczne wtrącenia w strukturze gotowego wyrobu. Stąd też jedna grupa producentów stosuje wypełniacz o dużej frakcji (znacznie tańszy), wychodząc z założenia że im więcej wtrąceń cząstek drewna tym większe złudzenie przypominające naturalny wygląd drewna na profilu.
Podczas gdy druga grupa producentów wykorzystuje mączkę o jak najdrobniejszej (dużo droższej) frakcji, dążąc do całkowitego wyeliminowania widocznych wtrąceń, jednocześnie całkowicie zabarwionej masy kompozytu. Warto dodać, że im większa frakcja mączki drzewnej, tym większa podatność na absorpcję wilgoci przez gotowy produkt.
Komponent "uzupełniający" - kreda
Najbardziej "ukrywany" składnik Kompozytu Drewna, pełniący również funkcję wypełniacza - tańszego wypełniacza. Jest to surowiec stanowiący niewielki udział procentowy całości składu komponentów WPC, jednakże z racji swojej niskiej ceny (w porównaniu do mączki drzewnej), chętnie stosowany przez niektórych producentów.
Niestety obniżając koszt produkcji, przy zastosowaniu w/w obniża się również jakość koloru gotowego produktu. Pod wpływem promieni UV, kreda zostaje "uwolniona" z masy, doprowadzając do znacznego wypłowienia koloru kompozytu drewna.
Koncentraty barwiące - MASTERBATCH
To tak na prawdę cały pakiet różnych składników poczynając od barwnika koloryzującego, kończąc na stabilizatorze UV. Tutaj nie powinno być kompromisów, należy stosować koncentraty najwyższej jakości, najlepszych producentów.
Komponenty wspomagające proces produkcyjny
Jest to grupa komponentów ułatwiających proces przetwórstwa tworzyw sztucznych, mająca duży wpływ na samą produkcję ale mniejszy na samą jakość produktu.
Na rynku polskim można znaleźć profile kompozytowe wyprodukowane w dwóch technologiach:
- Wytłaczania - ekstruzji
- Współwytłaczania - koekstruzji
Ekstruzja - wytłaczanie
Proces produkcyjny polegający na podgrzaniu wszystkich wyżej opisanych komponentów, doprowadzając do ich uplastycznienia, a następnie wytłoczenia całej powstałej masy pod wysokim ciśnieniem przez końcową głowicę nadającą odpowiedni kształt profili. Ta technologia umożliwia wyprodukowanie profili kompozytowych jednolicie zabarwionych w całej swojej masie, o najwyższych możliwych parametrach wytrzymałościowych równych właściwościom fizycznym masy produkcyjnej.
Koekstruzja - współwytłaczanie
Wstępny etap tego procesu produkcyjnego niczym nie różni się od powyżej opisanego procesu ekstruzji. Jednakże w tym rozwiązaniu produkcyjnym, do końcowej głowicy nadającej kształt profili, wtłacza się współbieżnie (jednocześnie) dwa rodzaje surowca.
W ten sposób powstaje profil dwuwarstwowy, zbudowany z rdzenia i otulającej ten rdzeń warstwy wierzchniej. Ten właśnie proces umożliwia stworzenie produktu hybrydowego - dwuwarstwowego.
Rdzenie profili wytworzonych w tym procesie wykonane są na bazie (PVC) o gorszej klasie odporności oraz obniżonych parametrach jakości i wytrzymałości. Zazwyczaj jest to masa nie barwiona lub lekko barwiona, o znacznie niższym składzie stabilizatorów UV. Tylko otulająca ten rdzeń warstwa wykonana jest z surowca o najwyższych parametrach odporności.
Kompozyt Drewna wytwarzany w procesie koekstruzji czyli "dwuwarstwowy" inaczej zwany kompozytem hybrydowym to mówiąc wprost - słaba jakość produktu ubrana w ładnie wyglądający garnitur. Garnitur, wykonany z najwyższej jakości komponentów, zabarwiony najwyższej jakości barwnikami czyli kompletnym surowcem, z którego tworzy się w całości Kompozyt Drewna metodą ekstruzji.
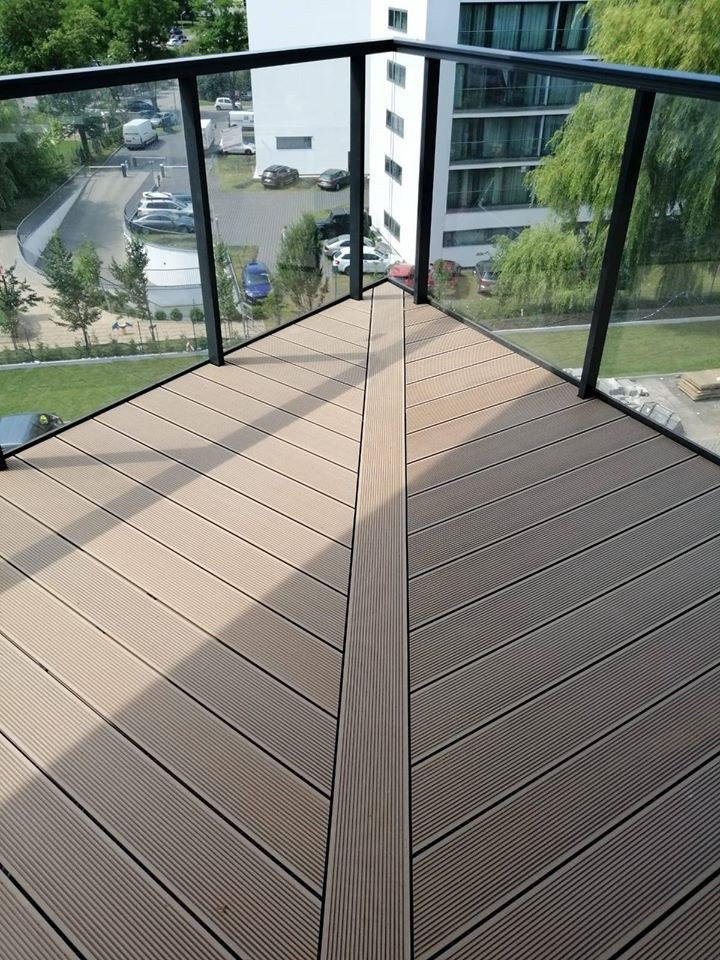
Tyle w teorii, teraz trochę praktyki...
Najczęściej produkowanym profilem z Kompozytu Drewna jest deska tarasowa. Można spotkać deski tarasowe o różnych wymiarach szerokości, grubości, sposobie wykończenia powierzchni, tzw. ryflowań. Równie jak szerokość deski nadawana jest przez producentów dowolnie, tak i sposób ryflowania jej powierzchni jest ich indywidualnym rozwiązaniem. Najczęstszą różnicę stanowi wysokość / grubość deski tarasowej kompozytowej. To właśnie ten wymiar profili jest mocno powiązany z procesem jego wytworzenia.
Bazując na normach oraz przyjętych założeniach prawa budowlanego, deska tarasowa z kompozytu drewna powinna posiadać odpowiednią odporność na uginanie się. Aby to osiągnąć, należy stworzyć deskę o odpowiedniej grubości w stosunku do jakości zastosowanego do jej produkcji surowca i jego fizycznych właściwości odpornościowych.
Łatwo jest zauważyć, że deski tarasowe z kompozytu drewna dostępne na rynku polskim mają różną grubość. Niemniej jednak równie łatwo jest znaleźć pewną zależność: deska jednowarstwowa (wykonana w procesie ekstruzji) ma zazwyczaj 21-22 mm grubości i to wystarczy do osiągnięcia normatywnej odporności i nośności.
Natomiast deski tarasowe hybrydowe to profile o grubości od 25 mm wzwyż (!). To właśnie jakość rdzenia wpływa na ich wytrzymałość, dlatego dla osiągnięcia wysokiej odporności na uginanie muszą być znacznie grubsze od jednowarstwowych desek tarasowych kompozytowych. Rozszerzalność termiczna takiego rdzenia jest znacznie wyższa od rozszerzalności otuliny, co prowadzi często do deformacji profili wykonanych tą metodą.
Artykuł opracowany przy udziale ekspertów EkoTeak.pl